Dimensional inspection of a product
Compliance with the dimensional specifications of mechanical parts is an important issue for their manufacturers. Dimensional inspection in industry relies on a variety of methods, each with its own advantages and limitations. By choosing the appropriate method based on part specifications and application requirements, manufacturers can guarantee the quality and conformity of their products, while optimizing their operational efficiency.

Why carry out dimensional checks on a product?
Dimensional inspection with the pneumatic method
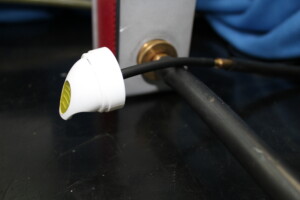
Dimensional checks using touch probes
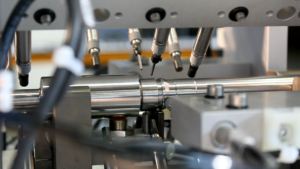
Dimensional inspection using industrial machine vision
Machine vision is an inspection method that uses cameras and advanced software to capture, record and analyze digital images of parts.
While its applications tend to focus on the detection of assembly or surface defects, it is also a fast, non-invasive dimensional measurement solution, making it particularly suitable for complex, delicate parts. It offers good accuracy and can be automated for high-throughput applications, improving the efficiency of manufacturing processes.
However, machine vision can be limited by variable lighting conditions or visual obstructions, which can affect the quality of the images captured and therefore the accuracy of the measurements made.
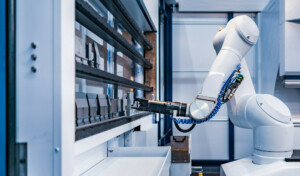
Dimensional checks using optical micrometry
Optical micrometry is similar to machine vision, but is based on the analysis of the shadow projected by the part to be inspected.
This technique generates images whose high contrast facilitates processing by imaging algorithms. Like machine vision, it enables rapid, non-intrusive measurements, ideal for checking the size of parts without altering them. Often integrated into automated systems , it is ideally suited to high-throughput applications. However, it is limited to measuring the dimensions of the external contours of inspected parts.
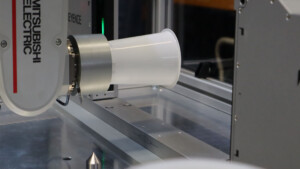
Dimensions control using X-rays
Industrial radiography is an inspection method that uses X-rays to check parts through their material. The resulting images are recorded and processed by image analysis software.
This method enables internal defects and dimensions to be identified with great precision, without damaging the part. It is particularly suited to opaque or thick materials where other measurement methods may be limited. Industrial radiography requires strict safety precautions due to the use of ionizing radiation.
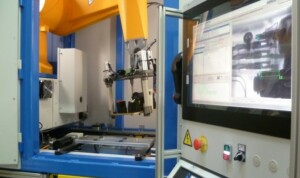
ASSOCIATED SETSMART TECHNOLOGIES
Visit the technology pages for more information on the control techniques used
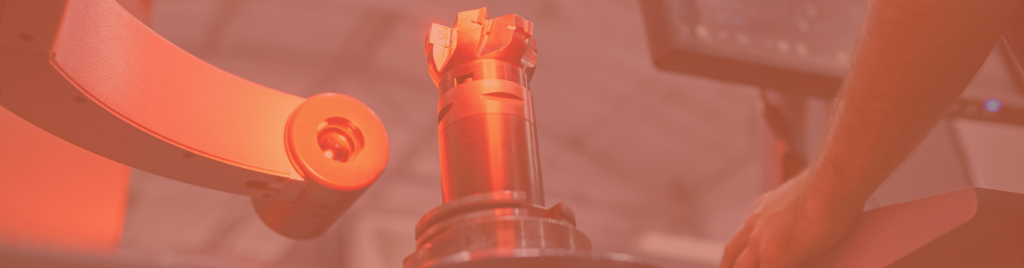