An overview of industrial radiography
Industrial radiography or X-ray inspection is a non-destructive method used to inspect the internal structure of assembled objects. It belongs to the family of techniques known as non-destructive testing, as it enables various control points to be checked without opening or breaking the object. The digitization of X-ray images and the image analysis software used make inspections both highly versatile and perfectly traceable.
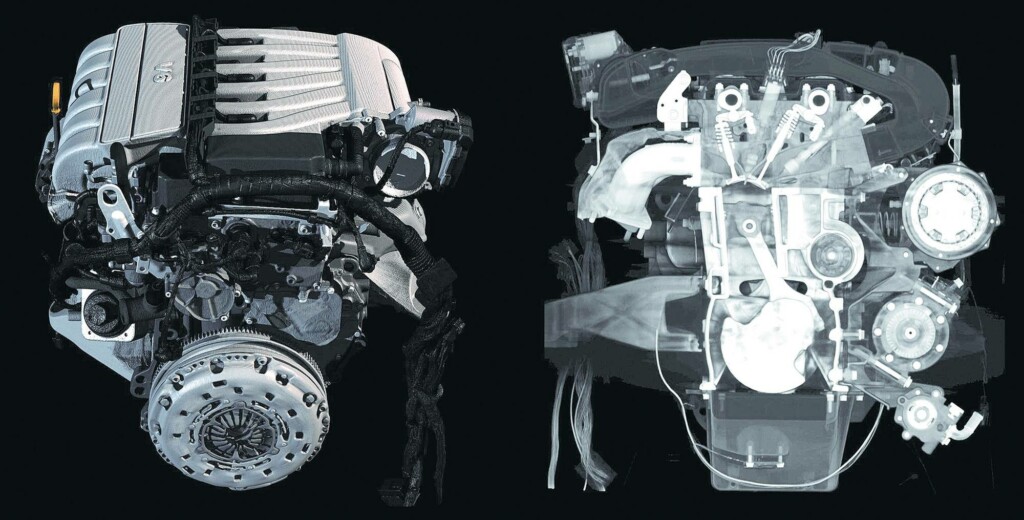
Introduction to X-ray inspection
This method relies on a system consisting of an X-ray source, a detector with a camera, image processing software and a radiation protection system (e.g. a lead cabin) to prevent operator exposure to harmful ionizing radiation.
In practice, the system usually also includes an automated object handling system, such as a robot.
Principle of industrial radiography
The assembled object to be inspected is placed between the X-ray source and the detector. X-rays can pass through most materials, but their absorption varies according to material type and thickness.
If an X-ray has passed through a metal part, for example, it will be more strongly absorbed than if it has passed through a plastic part. The detector, which is combined with a camera, therefore captures images whose contrast represents the degree of X-ray absorption. A metal part, such as a screw, attached to a plastic cover will thus appear white against a black background.
The image processing software identifies control points, using these contrasts to measure dimensions, check the presence or absence of sub-assemblies, proper assembly, the absence of foreign particles or material defects.
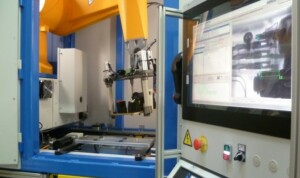
The benefits of Industrial radiography and X-ray inspection
The versatility of industrial radiography means it can be used to inspect a wide range of objects and control parameters. Particularly well-suited to inspecting internal dimensions, shapes, assembly and appearance, the technology ensures the delivery of compliant parts to customers.
Its non-contact nature is particularly advantageous for inspecting assemblies which, if opened, would be destructive or interfere with proper assembly. To a certain extent, it can therefore be applied to 100% production control. Once defined and programmed, controls become fast, reliable and durable, offering user-independent and autonomous capabilities.
The automation of measurement systems based on this technology brings a faster pace of work, as well as unrivalled precision and repeatability when it comes to handling objects and positioning them in front of the source. Alongside the use of lead structures and traps, these automated systems also help to protect operators from exposure to X-rays.
-
Versatile
Numerous inspection points can be performed on a wide range of inspection zones on the part
-
Non destructive
Internal control of the inspected object without having to open or dismantle it
-
Accurate and repeatable
Excellent metrological performance
-
Simple and fast
Measurements performed in seconds, independent of the user’s skills