Thickness measurement of a product
Thickness measurement is crucial in many industrial sectors. It provides information on product quality and performance, as well as on the associated manufacturing processes.
Simple tools such as thickness gauges are not suitable for all situations, especially when measuring in line or at high speed. The choice of an appropriate measurement technology will therefore depend on the specific properties of the material, the manufacturing process and the measurement requirements, with each method having its own advantages and limitations.
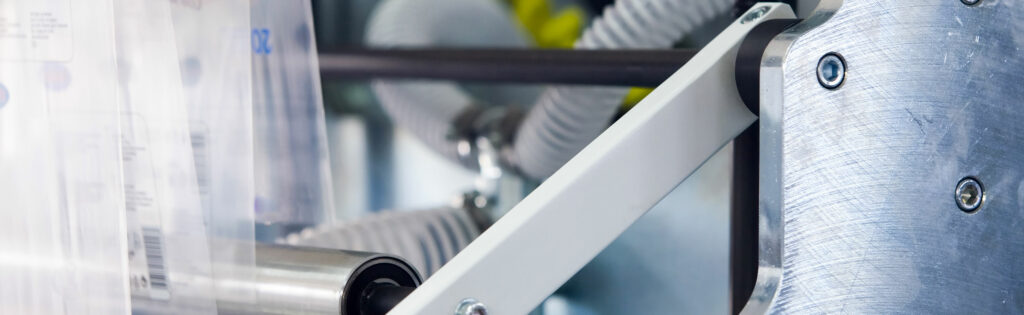
Thickness measurement: what for?
The importance of accurate thickness measurement in various industries, including film, strip (such as rubber) and packaging production, cannot be underestimated. Inadequate thickness of these materials can have significant repercussions on the quality and performance of end products, as well as on manufacturing processes.
Firstly, insufficient thickness can compromise the strength of products, making them more likely to deform or break under stress. Similarly, excessive thickness can affect the flexibility of materials, leading to difficulties when handling them or using them in production processes. In addition, inadequate thickness can affect product efficiency.
For example, in the food packaging industry, inadequate thickness can lead to problems with handling, storage, stacking, unstacking, and thus cause errors or blockages in automated handling processes, whether in the factory or in automatic devices for distributing food products to consumers.
Inappropriate thickness can also lead to excessive use of materials, resulting in additional raw material and manufacturing costs.
Therefore, reliable and accurate measurement methods must be implemented to control material thickness and adjust manufacturing processes, enabling the highest quality objectives to be achieved and production processes to be optimized.
Thickness measurement using touch probes
In the industry, LVDT (Linear Variable Differential Transformer) linear displacement transducers are widely used to accurately measure the thickness of objects. These sensors transform the linear movement of their probe into a measurable electrical signal, enabling their exact position on an axis to be tracked.
To measure the thickness of an object, two LVDT sensors are positioned on each side of the object to be inspected.
The two sensors are brought into contact with the object, and their position is recorded at the point of contact. The thickness is then deduced from the difference in position between the two sensors.
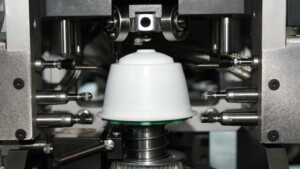
One of the main advantages of LVDTs for thickness measurement is their ability to provide accurate, reliable measurements, even in harsh industrial environments. They are robust, resistant to vibration and temperature variations, making them suitable for a wide variety of industrial applications.
The selection of probe tips is crucial for reliable measurements, taking into account their shape, size and material, while avoiding damage to the surface of the object under test.
LVDTs can also be easily integrated into automated quality control systems, enabling fast, accurate thickness measurements of objects in production.
Thickness measurement with the pneumatic method
Tracer sensor technology is based on the combination of a tactile sensor (LVDT) and a pneumatic transducer.
The pneumatic transducer is mobile and can continuously adjust its distance from the surface of the object to be measured to keep it constant. The LVDT precisely measures the movements of the pneumatic transducer, deducing variations in object thickness. Tracer sensors never touch the measured surface, making them a non-contact measurement tool.
The object can be placed on a reference surface, such as a roller for a rubber strip. The thickness is determined by the distance between this surface and the position of the tracking sensor.
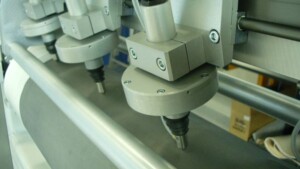
Alternatively, the measurement can be performed by a pair of tracking sensors placed on both sides of the object. The thickness is then deduced from the difference in position between the two tracer sensors.
These sensors offer micrometric precision over a wide measurement range. They are ideally suited to measuring the thickness of large parts such as plates, strips or films.
Unlike optical sensors, they are insensitive to the color, brightness or dirtiness of the material being monitored. Last but not least, tracer sensors can be integrated in line, so that thickness profiles can be determined continuously by using several in-line sensors.
Thickness measurement using optical micrometry
Optical micrometry is based on the analysis of the shadow projected by the object to be measured when illuminated by a light source. A special optical device is used to capture this shadow and generate a high-contrast image that facilitates processing by imaging algorithms.
Thickness measurement can be easily performed when the object is of a simple shape, such as a film or strip. In this case, the sensor is positioned laterally, generating an image of the shadow of the edge of the strip.
Alternatively, the strip can be placed on a roll, and the micrometer positioned perpendicular to the roll, at the edge of the strip. The micrometer then detects the shadow of both the roller and the strip. Its thickness is obtained by measuring the difference in height between the roller and the top surface of the strip on the image.
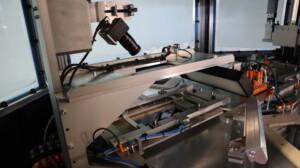
Frequently integrated into automated systems, this technology is well suited to high-speed applications. However, it is limited to measuring the dimensions of the outer contours of the film being inspected. Moreover, it can be sensitive to variations in brightness or to the cleanliness of the controlled material.
ASSOCIATED SETSMART TECHNOLOGIES
Visit the technology pages for more information on the control techniques used
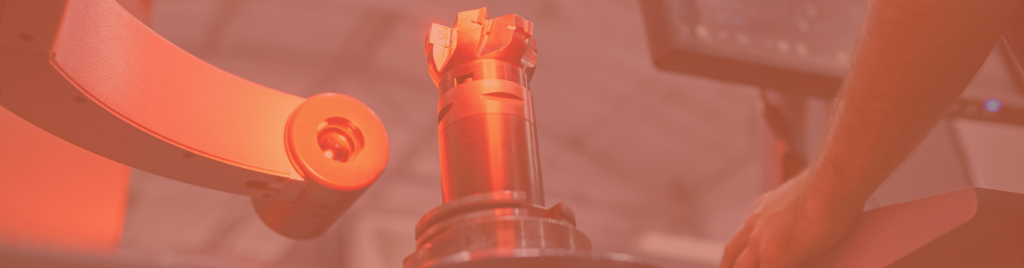