An overview of industrial automation in metrology
The aim of automation in industrial metrology is to increase the reliability of the inspections carried out, and therefore the quality and traceability of products, as well as the profitability of their manufacturing processes. Industrial automation technologies also help operators with some of their most exhausting and repetitive tasks.
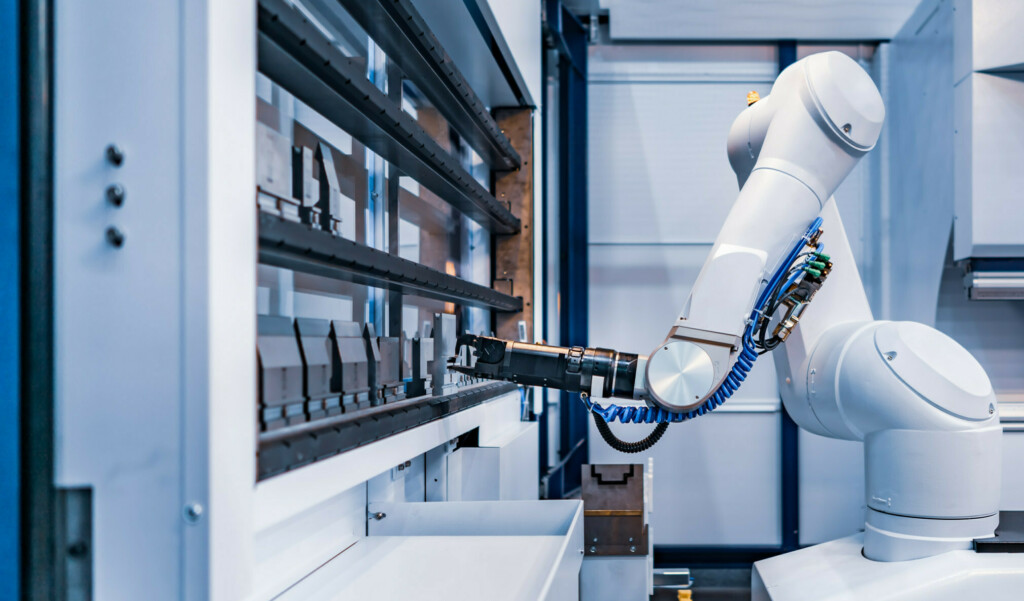
What automation technologies are we talking about?
By automation technologies, we mean systems for moving an object to be inspected, or a part of the inspection machine, with no action from an operator.
These technologies may be needed, for example, to position the object in front of a sensor, to hold it in front of a camera with the correct viewing angle, or to sort a group of objects prior to an inspection.
For example, robots, cobots, conveyors, rotating plates, automated lifting mechanisms, linear motion systems, vibrating bowls or other sorting systems can be designed and integrated into metrology or machine vision solutions.
Automation technologies: a focus on industrial robots
As industrial automation is highly diverse in nature, with a wide range of functions and uses, let’s focus on industrial robots.
Robots become essential when the movements the machine has to perform are complex and exceed the capabilities of simpler automation systems. Industrial robots can be categorized according to criteria such as number of axes of movement, working envelope, carrying capacity, as well as speed of operation, and positioning accuracy and repeatability.
- The number of axes determines the robot’s ability to move in space. In addition to simple translations in three dimensions, some robots can also perform various rotational movements. These can be used to rotate the object, or to move it in cluttered or hard-to-access areas of the machine.
- The working envelope defines the space accessible to the robot. The choice is mainly determined by the machine’s dimensions.
- Carrying capacity indicates the maximum weight a robot can lift and handle.
- Positioning accuracy and repeatability are essential criteria in metrology, as they characterize the robot’s ability to reach and constantly return to programmed positions. Operating speed is important for productivity. A compromise often has to be found between speed, accuracy and repeatability.
Finally, the robot must be equipped with the necessary tooling to perform the operation for which it is employed: for example, a prehensor, a gripper, a sensor or a manufacturing tool.
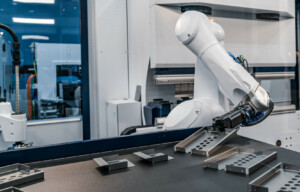
The benefits of automation in industrial metrology
The most obvious benefits of automation are in terms of cost savings and productivity.
A higher throughput: tasks are carried out rapidly, and despite certain unavoidable maintenance operations, automation technologies ensure continuous work.
Automation makes certain jobs less tedious, by sparing operators from repetitive tasks that can cause musculoskeletal disorders, especially when carrying heavy loads is involved. It also promotes more rewarding jobs by enabling operators to concentrate on more interesting, higher value-added tasks.
But in the field of metrology and production inspection, the advantages of automated systems also relate to the relevance of controls, and therefore ultimately to product quality. Indeed, the reliability of controls can be affected by incorrect positioning of the inspected object relative to the sensor. However, some industrial robots offer outstanding positioning performance, with accuracies better than +/-1 mm and repeatabilities better than +/-0.1 mm.
The use of industrial automation therefore ensures that quality measurements can be reproduced precisely and consistently.
-
Simple and fast
Technologies for high inspection throughput
-
Stand-alone operation
For unattended use
-
Accurate and repeatable
Support excellent metrological performance
Related products
-
Metrix GEO
For controlling the geometry of parts with well-specified shapes : straightness, perpendicularity, parallelism, roundness, coaxiality, etc.
-
Inspex OUT
For high throughput and precise inspection of the assembly, aspect, or surface finish of your products.